Part Datasheet Search > Voltage Regulators > ON Semiconductor > UC3845BVDR2G Datasheet PDF > UC3845BVDR2G Application Note Pages 1/8
UC3845BVDR2G Application Note - ON Semiconductor
Manufacturer: | ON Semiconductor |
Category: | Voltage Regulators |
Case Package: | SOIC-14 |
Description: | UC3845BVDR2G, PWM Current Mode Controller, 1A, 250kHz, 36V, 14Pin SOIC |
Pictures: |
UC3845BVDR2GDatasheet PDF
Page:
of 8 Go
If the format of the manual is confusing, please download and read the original PDF file.
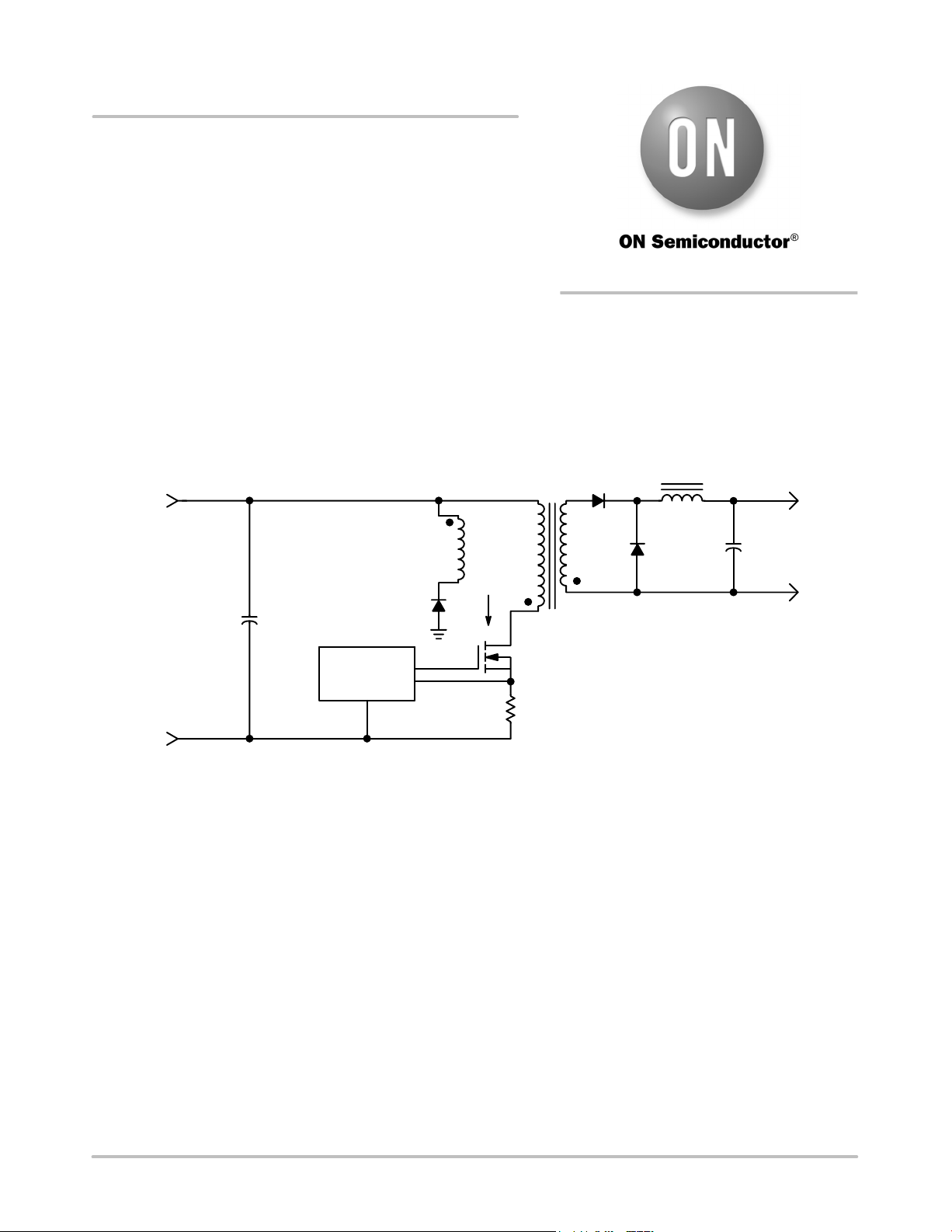
© Semiconductor Components Industries, LLC, 2005
August, 2005 − Rev. 1
1 Publication Order Number:
AND8039/D
AND8039/D
The One−Transistor
Forward Converter
Introduction
The one−transistor forward converter is the most
elementary form of transformer−isolated buck converter. It
is typically used in off−line applications in the
100 W − 300 W region. This application note illustrates the
approach one would take to design a high DC input voltage,
one−transistor forward converter. With additional
modifications, it could be made work as a 110 VAC off−line
power supply.
Description of Operation
A simplified schematic of a one−transistor forward
converter can be seen in Figure 1.
CONTROL
RESET
WINDING
C
IN
+
+
+
V
SW
−
I
SW
+V
IN
GND
D1
D2
L
O
+V
OUT
GND
C
OUT
Figure 1. Simplified Schematic of a One Transistor Forward Converter
One can see a transformer has been placed between the
input voltage and a buck converter output stage. The power
switch (SW) is used to create a rectangular voltage
waveform whose amplitude is the input voltage and its duty
cycle is the controllable variable. The transformer provides
both a step−up or down function and a safety dielectric
isolation between the input line and the output load.
The major restriction of this topology is the maximum
duty cycle must be about 50%. Whenever a core is driven in
a unidirectional fashion, that is, current only being driven
from one direction into the primary, the core must be reset.
Magnetization energy which serves only to reorient the
magnetic domains within the core must be emptied, or else
the core will “walk−up” to saturation after a few cycles. To
do this, one needs to reset the core. Resetting is done by
drawing current from a winding during the period when the
transformer is unloaded, that is, when the power switch and
rectifiers are not conducting. Any winding can provide the
reset function, but the higher the voltage on the winding, the
quicker the core will reset. Typically, this is the primary
winding or a separate reset winding of equal turns to the
primary. Current from the reset winding can then be returned
to the input capacitor and reused during the next cycle of
operation.
The typical switch voltage and current can be seen in
Figure 2. When the power switch is ON, the switch sees the
output filter inductor’s current reflected by through the
transformer. The amplitude of the primary current is the
output rectifier current times turns ratio of the transformer
(N1/N2) plus a small amount of magnetization current.
During the power switch OFF time, the switch voltage “flys”
up to about twice the input voltage. During this time, the
reset winding begins to output magnetization current back
to the input capacitor.
APPLICATION NOTE
http://onsemi.com
Part Datasheet PDF Search
72,405,303 Parts Datasheet PDF, Update more than 5,000 PDF files ervery day.